Overview
A loyal customer of Viking Pump® for 15 years, Stepan agreed to beta-test one of the latest pumps from our new Universal Product Line (4227C Series™) at their UK chemical manufacturing plant. Michael Smith Engineers was the local Viking Pump distributor, who initially approached Stepan as a likely pilot candidate due to a longstanding supplier-buyer relationship. Together, they set up the trial to demonstrate how this industrial-grade stainless steel, highly flexible modular design would operate in a demanding field application—outside the controlled conditions of a test laboratory.
Working with one of the world’s largest surfactant producers was an ideal proving ground, where corrosion resistance is of utmost importance and adopting new technology solutions for cost and efficiency savings is a high priority.
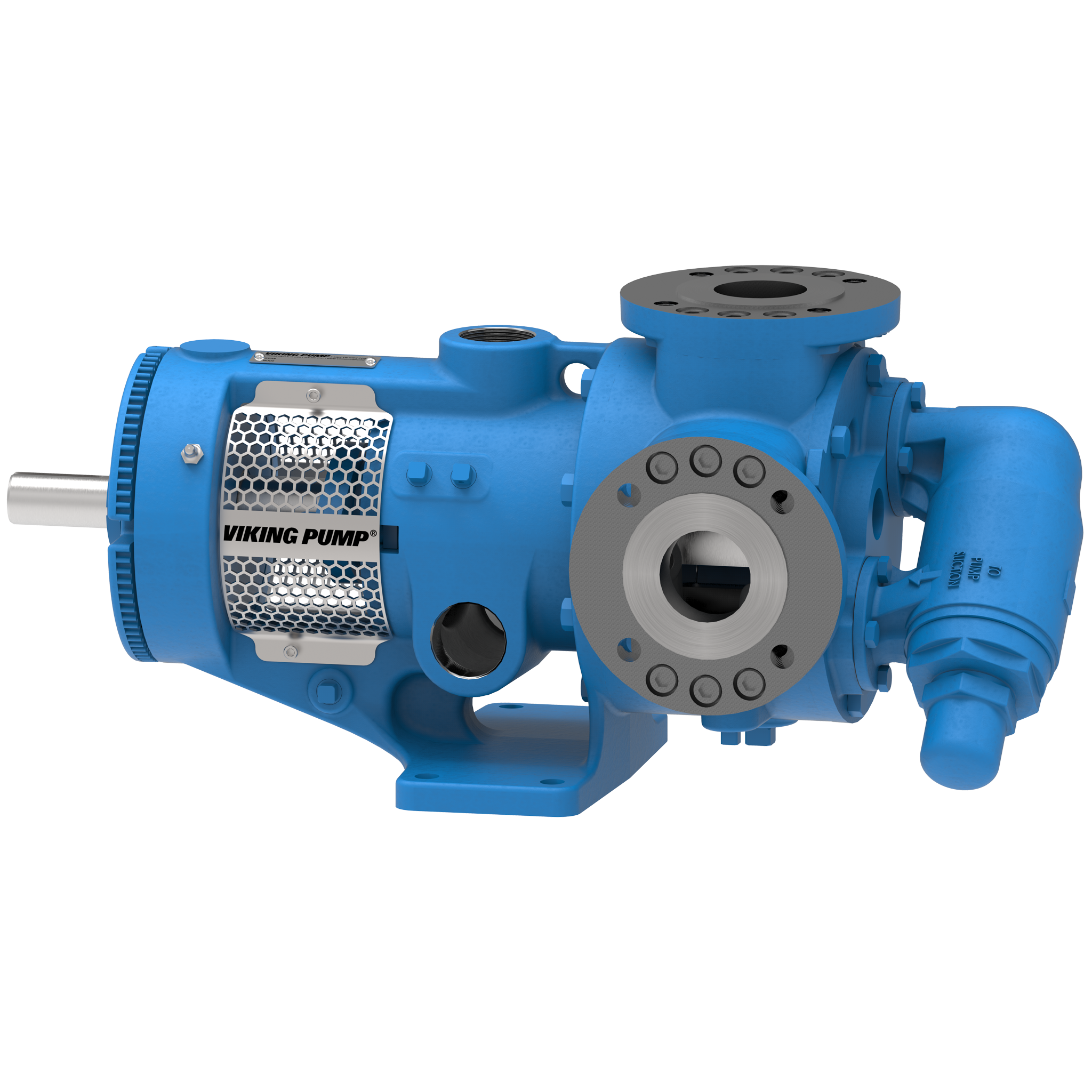
Challenge
In this test case, a replacement pump needed to meet, and exceed, Stepan’s high volumetric and performance requirements for a piping system through which surfactant ingredients flow. Using Viking Pump’s 4227C Series internal gear stainless steel pump, the trial’s objective was to validate the ease with which the innovative, modular design could be a drop-in-place solution; while also assessing the feasibility of interchangeable flanges enabling a universally sized pump. If it worked, this would mean decreased spares holding for the customer; thus, lowering the huge cost outlay traditionally associated with storing large inventories of various pump sizes.
Solution
The distributor collaborated with Stepan’s engineering team to connect the Viking 4227C pump to a 4-inch piping system integral to one of their chemical manufacturing processes. A standard 3-inch unit had been pre-fitted with 4-inch flanges so that the pump attached easily to the existing pipe configuration. Drawing from this most versatile line of internal gear pumps with many design and material options, certain choices were made to suit the particular scenario. For example, the pump was kitted for the 95-degree Celsius temperature maximum of the application that was using its own heating method (i.e. essentially lagging the discharge and suction lines). And to match the orientation of the pipework already in place, a 90-degree port option was selected (rather than a 180-degree port). Despite the Stepan team being very familiar and experienced with our pumps, Michael Smith Engineers remained on site to oversee the commissioning operation and ensure a seamless experience. In a matter of twenty minutes, the old pump was removed, and the new one dropped in perfectly. It took an additional two and a half hours to perform pump alignment checks and properly connect/align with the existing pipework. The customer was back up and running in just under three hours.
Advantages
As a beta tester, Stepan experienced these advantages first-hand before the leading-edge technology was released to the mainstream market:
- Stainless steel construction – provided corrosion resistance to harsh chemicals used in surfactant manufacturing
- Internal gear pump technology – enabled true positive displacement of a viscous liquid, with high volumetric efficiency
- Modular design – provided easy connection to existing pipework due to the flexibility of interchangeable flanges
- Onsite customer support – worked side-by-side with Stepan's team of engineers to ensure the pilot went smoothly
Business Results
Thanks to Stepan’s willingness to be a beta tester, we can call the trial a success in terms of efficacy in the field—efficiently pumping and running incident-free for nine months and still counting. That means no downtime and no leaks reported to date. Based on this outcome, the company plans to use Viking Pump’s modular series pumps for all of their replacements going forward. Such standardisation will cut costs significantly with the reduced spares holding. An added benefit of the modular Universal Product Line is Viking Pump’s reduction in the variety of different pumps being produced, which allows us to pass on more cost savings to the customer.
Viking Pump is committed to ongoing innovation, made possible in large part through trusted partnerships with companies like Stepan, to advance our capabilities and provide the right products for today’s pumping needs. It is also the valued customer relationships built by Michael Smith Engineers and other distributors that pave the way for conducting joint projects such as this one.
According to Steve Williams, Engineering Manager at Stepan UK, “With reliable service from MSE, Viking Pumps are a vital and integral part of our production plant. The changeout was seamless and the success of this trial meant it has gone under the radar. Through the advancement of Viking’s modular version of this rugged, robust pump, we will see future lifecycle costs reduced.”