It’s typically impossible to see inside pipes and tanks.
Industrial pipes are usually steel or stainless. Even the occasionally used PVC is typically opaque.
But on the day of this customer visit, they had a sight glass placed in a horizontal run of pipe which permitted a peek inside. Normally this glass was used to inspect the color and clarity of the product flowing by. But today the customer and myself were fixated on a hex nut that had made its way through the system and settled at the round bottom of the sight glass.
The nut would spin and slide and occasionally the flow rushing by would move it up the wall towards the outlet. Thankfully, the weight of the nut would cause it to slide back down to the bottom of the chamber. Today the nut didn’t leave the sight glass… But what about tomorrow, the next day, or beyond?
Between that sight glass and the pump… nothing. No strainer to act as a safety net to prevent the nut from entering the pump, locking it up, or worse- breaking the pump and resulting in a process shut down.
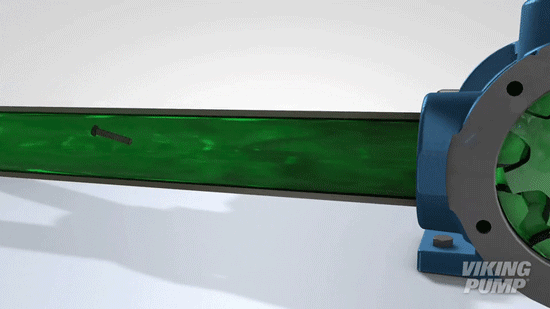
The potential outcome? Upwards of USD$100,000 a day at some customers in downtime alone. Plus the cost of pump repair, damage to downstream equipment, and contaminated product; the cost of inaction can be substantial.
Operating a pump without a strainer is like a trapeze act without a net. If all goes well, it won’t be needed. Unfortunately, in the real world all does not go well (see photo examples below). A strainer offers a low cost, highly reliable insurance policy to protect the pump and downstream equipment.
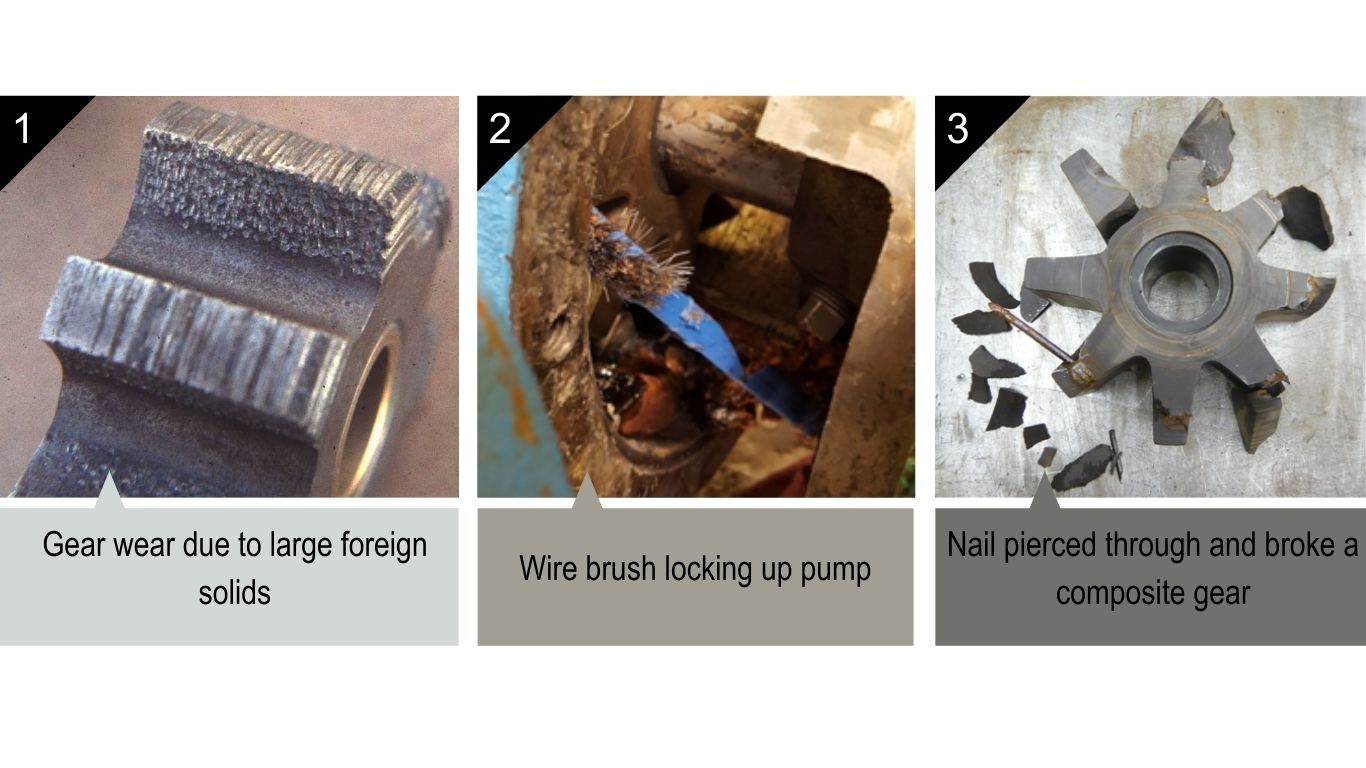
Left picture: gear wear due to large foreign solids. Middle Picture: Wire brush locking up pump. Right picture: Nail pierced through composite gear, breaking it.
Let’s be honest…strainers are not complicated devices. If you’ve ever made pasta, you’ve used a strainer. In simplest terms a strainer includes a plate or vessel with openings in it. These openings allow liquid to drain out, capturing anything too large to pass through.
For industrial strainers the underlying premise is the same, but this time it’s the liquid we want- not the solids. Pump strainers include either a perforated metal sheet or a wire mesh to allow the liquid to pass through. The opening size varies depending on the maximum size of solids allowed to pass.
Normally pump strainers are located in the suction piping before the pump. This ensures that foreign solids are captured before the liquid flows into the pump, protecting the pump and downstream equipment.
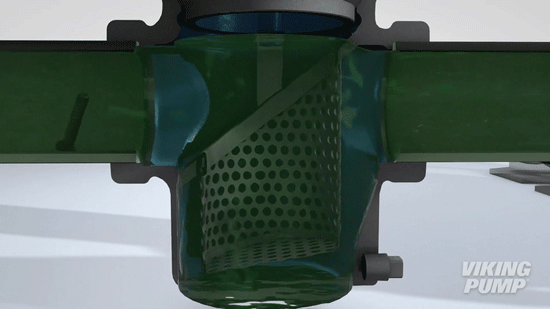
The most basic types of strainers are classified as Temporary Strainers. These typically consist of a perforated flat plate or cone that is placed between flanges in pipe. These are meant to be protection against any materials that may be present in a new installation. Because of the difficulty in installation and removal they are only used for short periods of time during the initial startup of a pump system.
While problems at startup are certainly more common, it’s not the only time that solids could be introduced to a pumping system. All 3 photos above happened to pumps long after startup. For this reason, Viking Pump strongly encourages the use of Permanent Strainers.
Permanent Strainers are designed to stay in the system through startup and day to day operation. Here are 3 of the most common types:
Y-Strainer (or wye strainer). These strainers take their name from the “Y” shape of the unit. They typically contain a cylindrical basket with moderate surface area. The basket is removable to allow for cleaning but would require the system to be shut down for cleaning and is cleaned from the bottom making them not ideal when frequent cleaning is required.
Simplex Basket Strainer. This is a single strainer which has a large basket area to collect material, thus reducing the frequency of cleaning. The basket is removed from the top, making cleaning easier and less messy than a y-strainer.
Duplex Basket Strainer. Duplex strainers have the same advantages as a simplex strainer, but with the added benefit of not requiring shut down for cleaning. A built-in diverter valve allows from to be shifted from basket to basket allowing a dirty basket to be cleaned out without shutting down the system.
Ferrous Traps offer another means of separating solids from a liquid. If ferrous particulate is present it will collect on magnets which can be cleaned later. These may be magnetic inserts used along with a mesh strainer or for extremely high viscosity liquids, like chocolate, may not use a basket at all.
Step 1. Select the type. For Viking Pump installations all types have been used, but most common would be simplex basket strainers. The decision will largely depend on the cleaning frequency requirements.
Step 2. Select a model size. Normally this matches the suction line size, connection type, and materials of construction. For example, for 2”, flanged, stainless steel suction lines, a 2”, flanged, stainless steel strainer would be the most likely selection. Additionally, the lid is normally sealed with an o-ring so elastomer compatibility with the liquid may need to be confirmed (normally this has already been done for pump seals anyway).
Step 3. Basket selection. This is a critical step. If the opening size is too large, then damaging particles will still get through. If the opening size is too small then the basket may require overly frequent cleaning, or worse, the pressure drop across the basket may create an NPSH problem for the pump.
For Viking Pump the most basic offering is a perforated basket. Openings vary from 5/32” to 3/16” (see photo 4) depending on the strainer size. While smaller particulate will easily pass through, this is typically adequate protection against large foreign objects such as tools, safety glasses, pens, bags etc. This would protect against the failure examples in photos 2 and 3 above. This also has the advantage of a very low pressure drop across the basket.
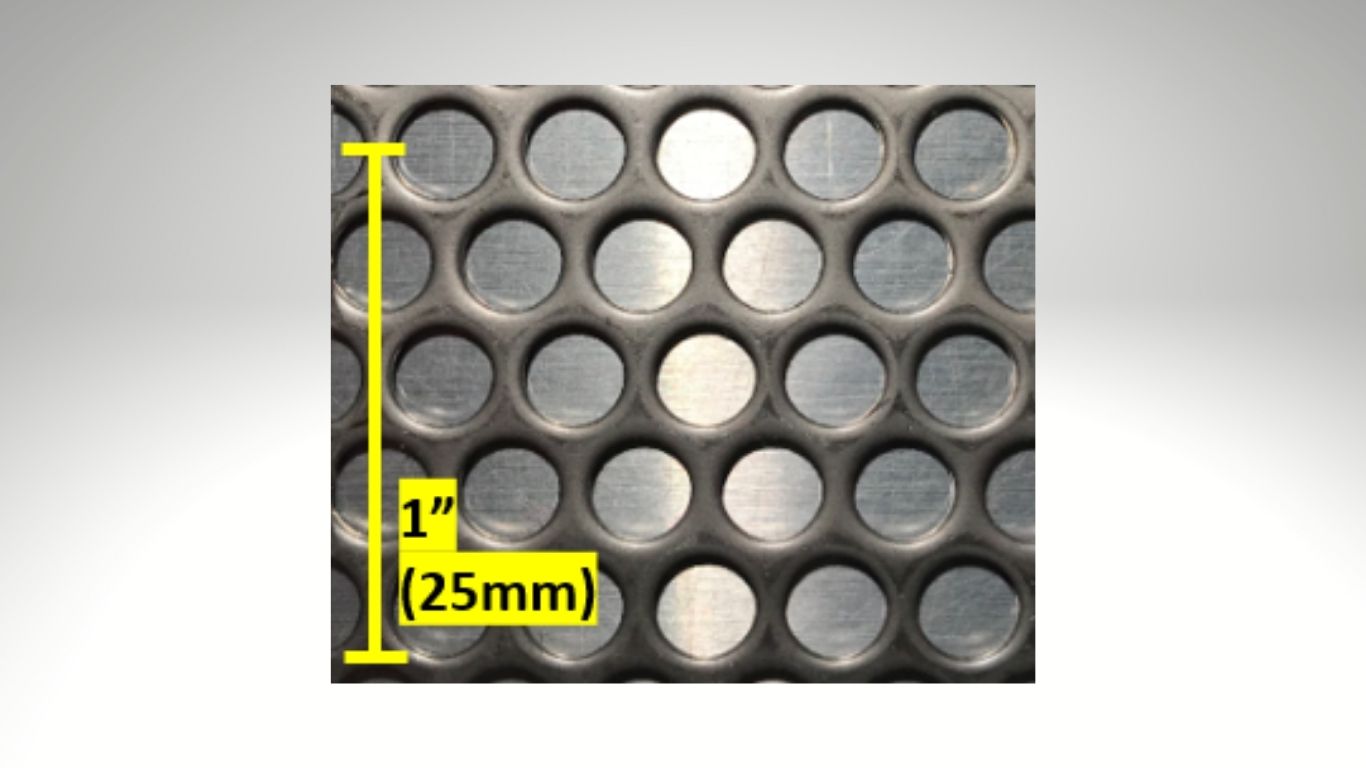
For additional protection, Viking Pump offers mesh baskets. These use the same “no mesh” perforated baskets for structure but include a mesh liner that is welded in place. Mesh baskets are given a number based on the number of wires per inch. As an example, a 10 mesh basket features 10 wires vertically and 10 wires horizontally per square inch (see photo 5 below). Viking Pump offers a variety of mesh sizes from 10 to 100 mesh. A chart of these sizes along with the opening size is below.
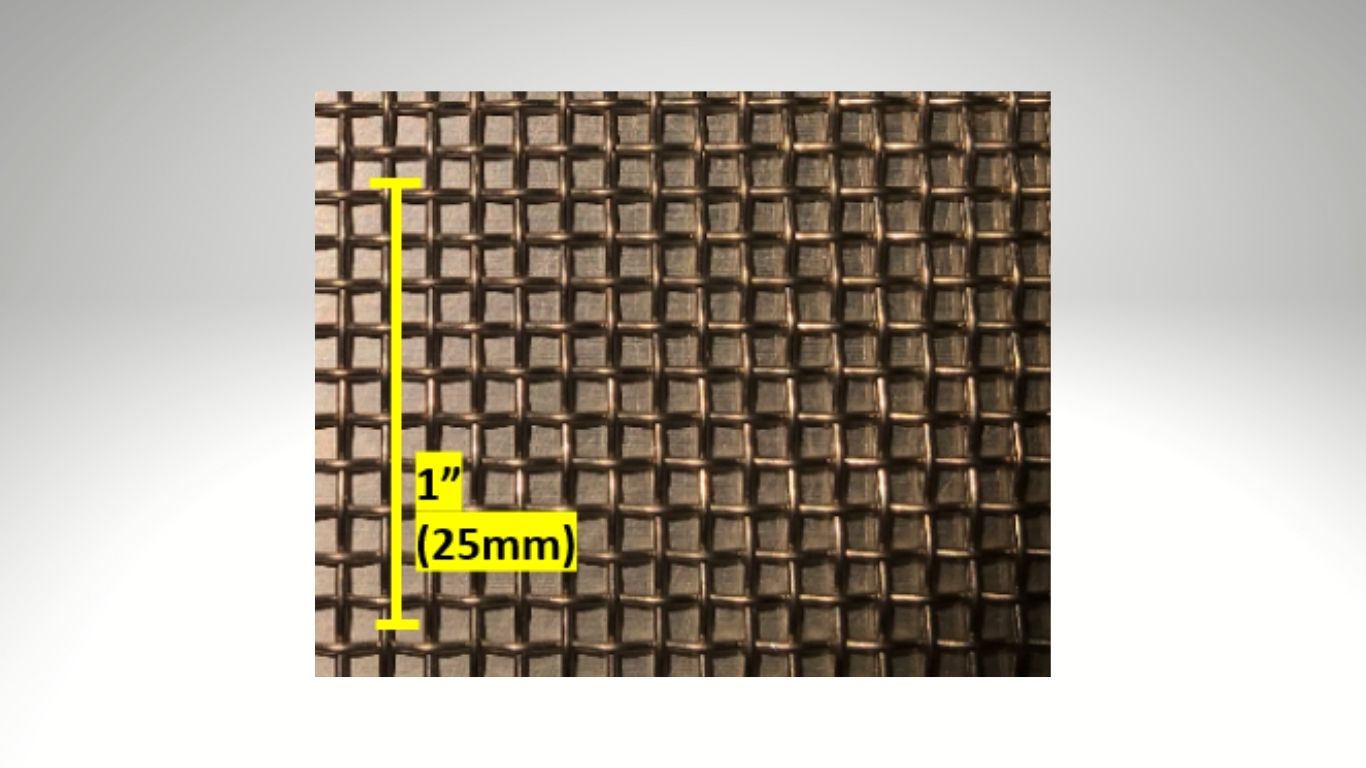
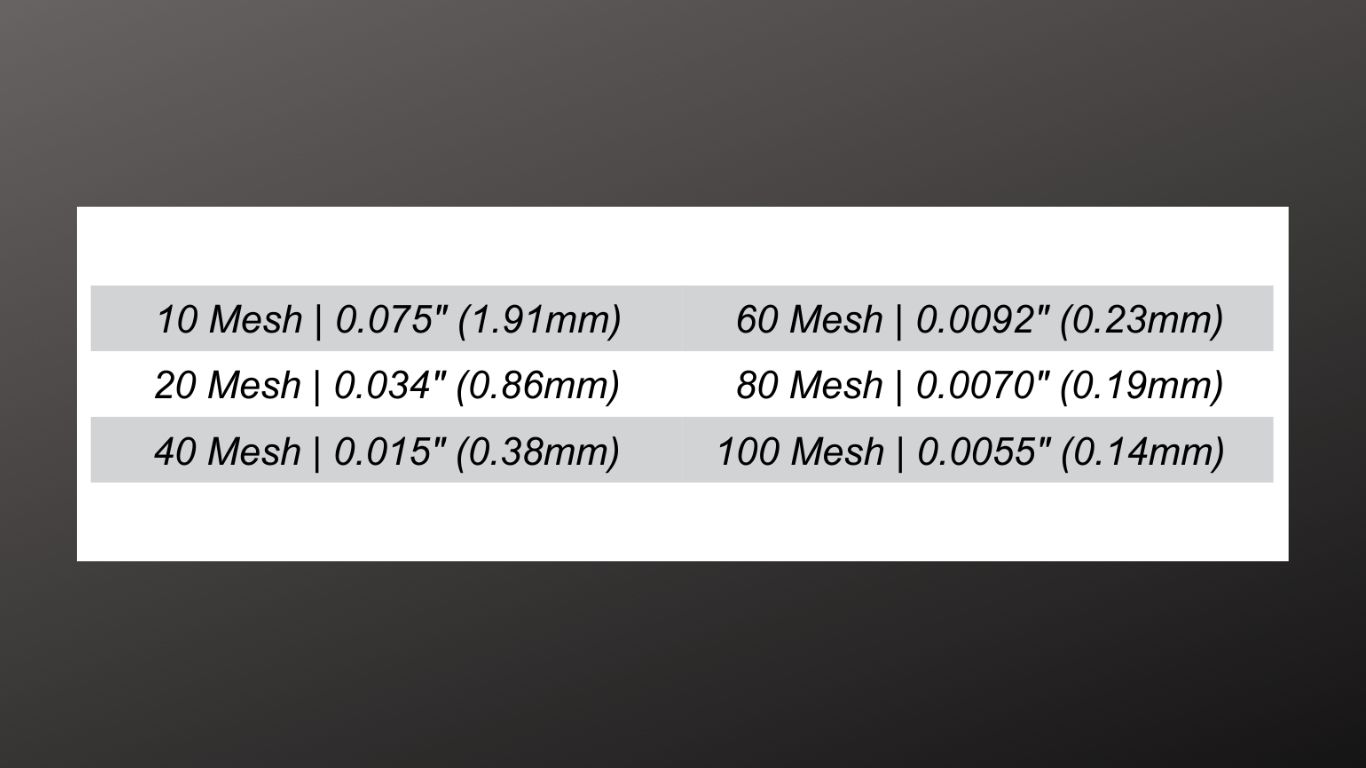
When selecting a mesh size, it’s important to consider how much restriction this puts on the suction side of the pump. For thin liquids a fine mesh may be suitable but for more viscous applications a larger opening may be required. In some cases, if an application is both viscous and a tighter mesh is required then a larger strainer may be used to increase the open area and decrease the pressure drop. Viking Pump provides selection curves to calculate the pressure drop across a clean basket.
Installation of gauges or differential pressure indicators at the strainer can help to identify when a strainer needs cleaning. A dirty basket will have a higher differential pressure across it.
Make sure the strainer is accessible for cleaning. If it’s difficult to access, then it’s less likely to be cleaned.
For suction side strainers it’s recommended to limit the pressure drop to 2 PSI or less. Remember, that’s for a clean basket. As the basket becomes dirty, the pressure drop will rise and can lead to NPSH problems and cavitation.
Having an extra strainer basket can expedite cleaning and reduce downtime.
Strainers (or even filters) are also found downstream after the pump. This can allow for tighter filtration and help to ensure a clean final product.