Viking Pump’s new generation of internal gear pumps (sizes H-QS in steel and stainless steel) offer a wide array of benefits that the previous alloy pumps could not, particularly in the area of porting flexibility. These new pumps reduced the number of casing configurations, which helps reduce manufacturing complexity, cost and lead times, while at the same time increasing the number of porting options and providing greater porting flexibility.
Because of the wide range of viscosities that a Viking pump can handle, our users told us they want the option of having smaller ports for low viscosity liquids to reduce piping costs, or of having much larger ports for high viscosity liquids, to reduce friction losses and therefore power requirements. That meant that a given size pump had to have multiple port size options, as well as ports conforming to different global standards and pressure/temperature ratings.
One of the key reasons for the many casing configurations that Viking Pump produced in the past was that the ports were integrally cast into the casing, which meant that every pump size had unique casings for each port size, standard and rating option. This resulted in a proliferation of casings to satisfy every need globally.
The Viking Pump ProPort™ Casing
One of the major changes that led to the new ProPort™ casings is that it uses bolt-on instead of cast-in ports. This enabled reducing the number of unique casings from 372 to 14. That bears repeating – going from 372 unique casings to 14. That enables distributors to inventory a range of sizes with the ability to quickly change ports to satisfy their customers unique piping arrangements.
For example, the new K and KK size pumps offer bolt-on 2” NPT ports; ANSI-compatible Class 150 raised-face flanges in 2”, 2-1/2”, 3” and 4” sizes; Class 300 in 2”, 2-1/2” and 3” sizes; as well as DIN 50, 65 and 80 PN16 ports. So now instead of many casings, one casing, used on both K and KK sizes, has 11 bolt-on port options, with internal porting sized to accommodate the largest available port. See the table below for available ports.
Port Options (Inches) | Pump Sizes | ||||||||
---|---|---|---|---|---|---|---|---|---|
H | HL | K | KK | L | LL | LS | Q | QS | |
1.5" NPT | S | S | |||||||
2" NPT | ✔ | ✔ | ✔ | ||||||
1.5" Class 150 ① | ✔ Ⓡ | ✔ Ⓡ | |||||||
1.5" Class 300 ② | ✔ Ⓡ | ✔ Ⓡ | |||||||
2" Class 150 ① | ✔ | ✔ | S Ⓡ | S Ⓡ | |||||
2" Class 300 ② | ✔ | ✔ | ✔ Ⓡ | ✔ Ⓡ | |||||
2.5" Class 150 ① | ✔ Ⓡ | ✔ Ⓡ | S Ⓡ | ||||||
2.5" Class 300 ② | ✔ Ⓡ | ✔ Ⓡ | ✔ Ⓡ | ||||||
3" Class 150 ① | ✔ | ✔ | ✔ Ⓡ | S Ⓡ | S Ⓡ | ||||
3" Class 300 ② | ✔ | ✔ | ✔ | ✔ Ⓡ | ✔ Ⓡ | ||||
4" Class 150 ① | ✔ Ⓡ | ✔ Ⓡ | ✔ | ✔ | ✔ | S Ⓡ | |||
4" Class 300 ② | ✔ | ✔ | ✔ | ✔ Ⓡ | |||||
6" Class 150 ① | ✔ | S Ⓡ | |||||||
6" Class 300 ② | ✔ | ✔ Ⓡ | |||||||
DIN 32 PN16 * | ✔ Ⓡ | ✔ Ⓡ | |||||||
DIN 40 PN16 * | ✔ | ✔ | |||||||
DIN 50 PN16 * | ✔ | ✔ | ✔ Ⓡ | ✔ Ⓡ | |||||
DIN 65 PN16 * | ✔ | ✔ | ✔ | ✔ Ⓡ | |||||
DIN 80 PN16 * | ✔ | ✔ | ✔ | ✔ Ⓡ | ✔ Ⓡ | ||||
DIN 100 PN16 * | ✔ | ✔ | ✔ | ✔ Ⓡ | ✔ Ⓡ | ||||
DIN 150 PN16 * | ✔ | ✔ Ⓡ |
✔= Available Port Option
S = Standard Porting
Ⓡ = Flanges designed with a Raised Face
① = Ports are suitable for use with Class 150 steel or stainless steel companion flanges or flanged fittings
② = Ports are suitable for use with Class 300 steel or stainless steel companion flanges or flanged fittings
* Ports are suitable for use with DIN PN16 steel or stainless steel companion flanges or flanged fittings
Fig. 1 - Port Options for ProPort™ Casings
Key Benefits of ProPort™ Casings
In addition to the flexibility, lead time and price reduction benefits, here are some additional reasons for changing to the Modular pumps’ ProPort™ Casings:
- The removable NPT threaded ports on H-L size pumps eliminate the need for unions in the suction and discharge lines that were previously required to remove an NPT-ported pump.
- Since all ports can be re-used, if a replacement pump is needed it can be ordered less ports to further reduce cost.
- The bolt-on ports can be sealed by gaskets or O-rings, and were designed and tested to ensure nozzle load ratings exceed ASME, DIN and other standards globally.
- Your distributor can provide enlarged suction ports to minimize friction losses that decrease NPSHa and can cause cavitation, while using smaller sized discharge ports to keep piping costs low.
Viking pumps are known for mostly having 90⁰ ports, usually to enable side suction, top discharge piping, to pump to overhead lines, though casings are rotatable for other arrangements. Some customers had expressed desires for more opposite port options, and while some opposite port models were available, they were usually with longer lead times and higher prices. Unbelievably, in reducing the number of casings from 372 to 14, Viking Pump actually added opposite port models in all sizes, H through QS (with capacities from 30 to 500 GPM or 3.5 to 114 m3/hr). That’s 26X fewer casings, with more customer-focused options! And the new casings are completely retrofittable onto existing Viking pumps.
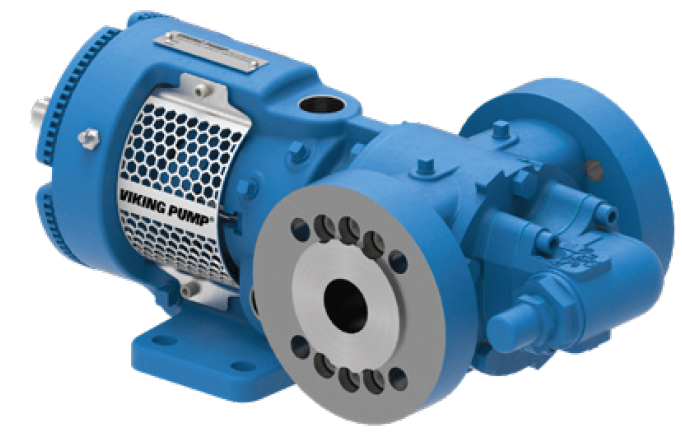
More Features in Every Casing
First, Viking Pump’s alloy pumps had long used gaskets to seal the bracket and head to the casing, since gaskets were compatible with almost every liquid, and simplified product selection. Some customers preferred O-ring seals, however, which meant machining special grooves at higher cost and longer lead time. The new ProPort™ casings are gasketed, but also have O-ring grooves standard to enable static O-ring seals if required.
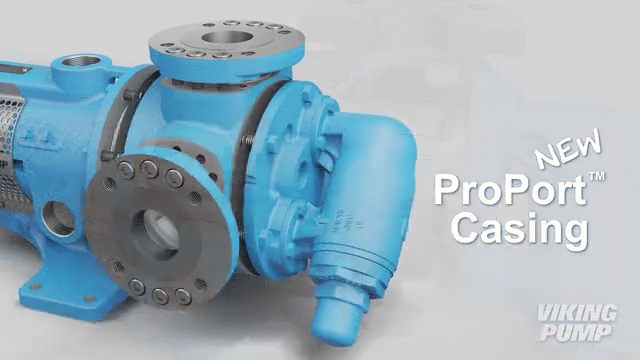
Second, casing drains were formerly optional and added cost and lead time, but are now standard, enabling near-complete draining before removing a pump for maintenance. This enhances operator safety and minimizes any spilled liquid on site.
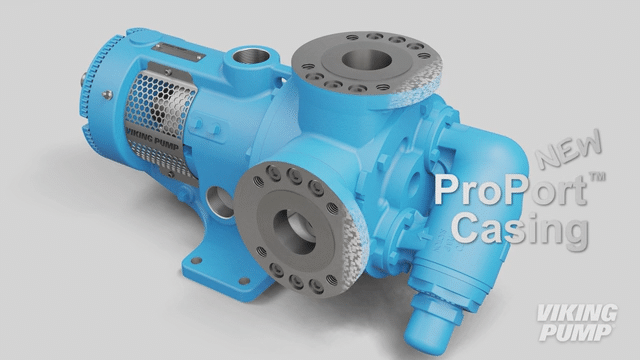
And finally, some customers required custom-machined flush and/or suckback grooves to promote a small amount of flow behind the rotor, to prevent materials like latex or chocolate from setting up there. The new casings feature drilled holes from the suction and discharge ports to the area behind the rotor, plugged with removeable setscrews as standard, to allow users to experiment with the best combination of flush and/or suckback if needed.
If the ProPort™ casings weren’t amazing enough, see the Modular Pump Overview blog and the upcoming blog on the U-Plus™ modular brackets and the sealing flexibility they provide!
Watch our Quick Tip video on the ProPort™ Casing below:
About the Author
John Hall has held marketing, sales, and technical management roles for several pump manufacturers, including 23 years at Viking Pump before retiring in 2023. He holds a B.S. in Technical Communications and an MBA in Marketing Management from the University of Minnesota.