As a masterclass in engineering design and manufacturing flexibility, Viking Pump has re-designed its heavy-duty alloy pumps, both steel and stainless steel, in the most ingenious ways. These new models reduce price and lead time by significantly reducing the number of casings and brackets for manufacturing simplification, while simultaneously providing more options for porting and shaft sealing, all while adding many great new standard features.
Best of all, the new pumps are interchangeable, both dimensionally and performance-wise, with Viking’s existing steel 123A, 4123A, 223A, and 4223A series, and the stainless steel 127A, 4127A, 227A and 4227A series, and the 724 and 4724 series which they will mostly replace.
The new modular pumps have similar model numbering to the previous generation, but end in “C” instead of “A.” See the full range of Viking Heavy Duty pumps below (fig. 1), with the new modular pumps shown in red.
Size | |||||||||||||||||
---|---|---|---|---|---|---|---|---|---|---|---|---|---|---|---|---|---|
Material | Jacketing | Series - Seal Type | F | FH | G | H | HL | K | KK | L | LL | LS | Q | QS | N | R | RS |
Steel | Non- Jacketed | 123C - Packed | ✔ | ✔ | ✔ | ✔ | ✔ | ✔ | ✔ | ✔ | ✔ | ||||||
4123C - Mech. Seal | ✔ | ✔ | ✔ | ✔ | ✔ | ✔ | ✔ | ✔ | ✔ | ||||||||
Jacketed | 223C - Packed | ✔ | ✔ | ✔ | ✔ | ✔ | ✔ | ✔ | ✔ | ✔ | |||||||
4223C - Mech. Seal | ✔ | ✔ | ✔ | ✔ | ✔ | ✔ | ✔ | ✔ | ✔ | ||||||||
323A - Packed | ✔ | ✔ | ✔ | ||||||||||||||
4323A - Mech. Seal | ✔ | ✔ | ✔ | ||||||||||||||
Max. Flow | GPM | 15 | 30 | 75 | 100 | 135 | 140 | 200 | 300 | 500 | 600 | 1100 | 1600 | ||||
m³/h | 3.4 | 6.8 | 17 | 23 | 31 | 32 | 45 | 68 | 114 | 136 | 250 | 363 | |||||
Max. Speed | RPM | 1750 | 1750 | 780 | 780 | 640 | 520 | 640 | 520 | 520 | 350 | 280 | 280 | ||||
Stainless Steel | Non- Jacketed | 127C- Packed | ✔ | ✔ | ✔ | ✔ | ✔ | ✔ | ✔ | ✔ | ✔ | ||||||
4127C - Mech. Seal | ✔ | ✔ | ✔ | ✔ | ✔ | ✔ | ✔ | ✔ | ✔ | ||||||||
1127C - O-Pro® Seal* | ✔ | ✔ | ✔ | ✔ | ✔ | ✔ | ✔ | ✔ | ✔ | ||||||||
Jacketed | 227C - Packed | ✔ | ✔ | ✔ | ✔ | ✔ | ✔ | ✔ | ✔ | ✔ | |||||||
4227C - Mech. Seal | ✔ | ✔ | ✔ | ✔ | ✔ | ✔ | ✔ | ✔ | ✔ | ||||||||
1227C - O-Pro® Seal | ✔ | ✔ | ✔ | ✔ | ✔ | ✔ | ✔ | ✔ | ✔ | ||||||||
327A - Packed | ✔ | ✔ | ✔ | ||||||||||||||
4327A - Mech. Seal | ✔ | ✔ | ✔ | ||||||||||||||
724 - Packed | ✔ | ✔ | ✔ | ||||||||||||||
4724 - Mech. Seal | ✔ | ✔ | ✔ | ||||||||||||||
Max. Flow | GPM | 1.5 | 3 | 5 | 10 | 20 | 50 | 65 | 90 | 110 | 160 | 200 | 320 | 600 | 1100 | 1600 | |
m³/h | 0.3 | 0.7 | 1 | 2.3 | 4.5 | 11 | 15 | 20 | 25 | 36 | 45 | 73 | 136 | 250 | 363 | ||
Max. Speed | RPM | 1750 | 1750 | 1150 | 1150 | 1150 | 520 | 520 | 420 | 420 | 520 | 350 | 350 | 350 | 280 | 280 |
*Speeds with some O-Pro® seal models are derated vs. packed or mechanical seal models. Max O-Pro® speed on H & HL are 760 RPM, N is 280 RPM and R &RS are 225 RPM
Fig. 1 – Viking Heavy Duty models with new Modular pumps shown in Green.
Addressing the Big Question: Why?
Why would Viking Pump change its highly successful range of alloy pumps? The existing series are workhorse internal gear pumps used across the chemical, general industrial and food processing industries.
But with literally tens of thousands of possible configurations, it was difficult for Viking distributors to predict and inventory exactly what their customers would need. So if a pump user wanted a particular configuration they either had to wait for a bespoke pump or were forced to accept tradeoffs - a pump with whatever feature set was available in stock at the local distributor.
That meant that most alloy pumps were built to order, and building unique one-off pumps is inefficient, even for a vertically-integrated manufacturer like Viking Pump with its own foundries. Lead times were usually longer than customers wanted and were even more pronounced for European and Asian customers due to ocean shipping, which was unacceptable.
So through modular design, Viking Pump distributors can now inventory key components and build up whatever configurations their customers need, greatly reducing lead times while simultaneously reducing prices and adding new features.
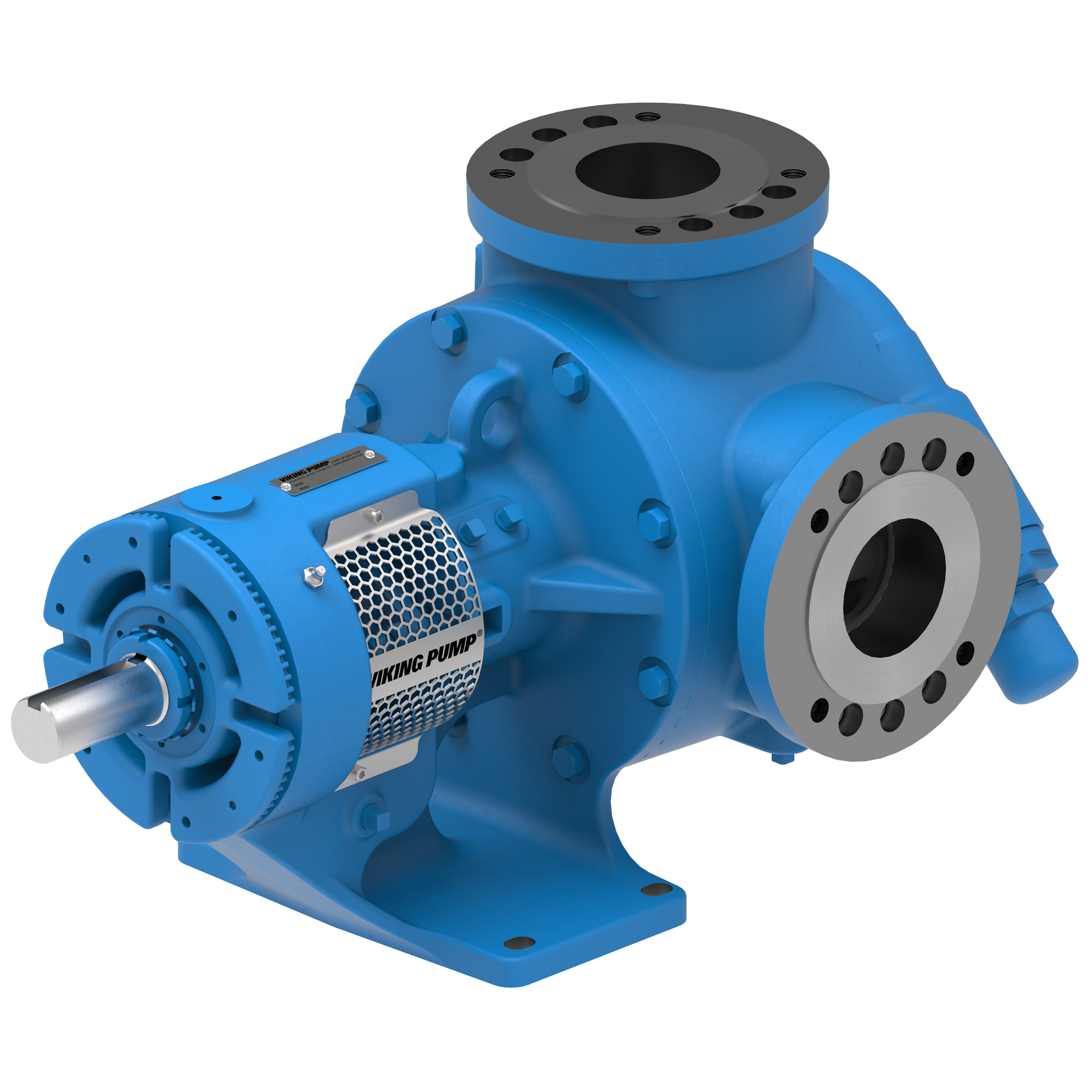
Stainless Steel
The stainless steel pumps are primarily used for:
- Corrosive chemicals (e.g. acids and bases).
- Any process where the pumps will be flushed with water or steam (e.g. sugar processing).
- Low-hazard food processing (e.g. edible oils).
- Very low temperature processes to -120⁰F / -85⁰C (e.g. silicone oil in freeze dryers)
- For use outdoors in very cold climates.
Steel
The steel models are generally used for:
- Flammable or hazardous liquids (e.g. fuels, petroleum and petrochemicals) where thermal cracking of iron would be a concern in the event of a fire-fighting water deluge.
- Very high temperatures to 800⁰F / 430⁰C (e.g. heat transfer fluids, pitch, polystyrene) where iron or stainless steel is not suitable.
You can find details regarding the new modular pump designs in future blogs covering their key components: the new ProPort™ casings and the new U-Plus™ brackets.
About the Author
John Hall has held marketing, sales, and technical management roles for several pump manufacturers, including 23 years at Viking Pump before retiring in 2023. He holds a B.S. in Technical Communications and an MBA in Marketing Management from the University of Minnesota.