Given that there were tens of thousands, if not hundreds of thousands of the dynamically sealed Viking heavy duty pumps operating in the field, Viking engineers were repeatedly challenged to make a sealless mag drive pump that could be a drop-in replacement for those existing pumps, meaning able to use the same baseplate, motor, gear reducer and piping. The goal would be to simply unbolt the old and bolt in the new.
This challenge resulted in the Universal Mag Drive (UMD) Series to simplify the upgrade process for existing dynamically sealed pumps to sealless mag drives. The performance of the UMD pumps is virtually identical to that of their equivalent sealed models, and perhaps even more important is that the footprint, or key mounting dimensions, are identical as well. This enables users to simply unbolt an existing sealed pump and "drop-in" an equivalent sealless pump without modifying the piping or drive system.
Old vs New
Shouldn’t new models always be better that their predecessors? The UMD certainly is. As Viking’s 4th generation of mag drives, it represents state-of-the-art technology in heavy duty, leak-free and fugitive-emission-free pumping technology. Let’s take a look at what makes these pumps so special.
Flexible
The Universal Mag Drive, or UMD, is interchangeable with Viking Pumps heavy duty dynamically-sealed (e.g. 124A/123A/127A model) pumps, as well as the old 125/123/127 and 124 series pumps. The same casing, head and idler are used throughout, providing parts interchangeability for users of all of these models.
Materials of Construction | Pump Series Nomenclature | |||
---|---|---|---|---|
Packed Gland | Mechanical Seal | O-Pro® Seal | Universal Mag Drive (UMD) | |
Cast Iron | 124A | 4124A | 1124A | 8124A |
Steel | 123A | 4123A | 1123A | 8123A |
Stainless Steel | 127A | 4127A | 1127A | 8127A |
Fig. 1 - Pump Series Nomenclature
Increasing Reliability While Preventing Leakage and Fugitive Emissions
The whole point of a mag drive is to eliminate leakage and fugitive emissions during normal operation. The UMD does this by using static O-ring seals to seal the head to the casing, the casing to the adapter plate, and the adapter plate to the canister, as shown in Fig 2 below.
These elastomeric static seals are not subject to wear, unlike dynamic seals like packing, lip seals or mechanical seals. Since seal leakage is the single greatest cause of pump downtime, eliminating dynamic seals greatly increases the Mean Time Between Failures (MTBF), an extremely helpful side benefit. And since unplanned downtime is usually the largest component of pump Life Cycle Cost (LCC), investing in sealless technology usually pays big dividends based on increased pump and process reliability.
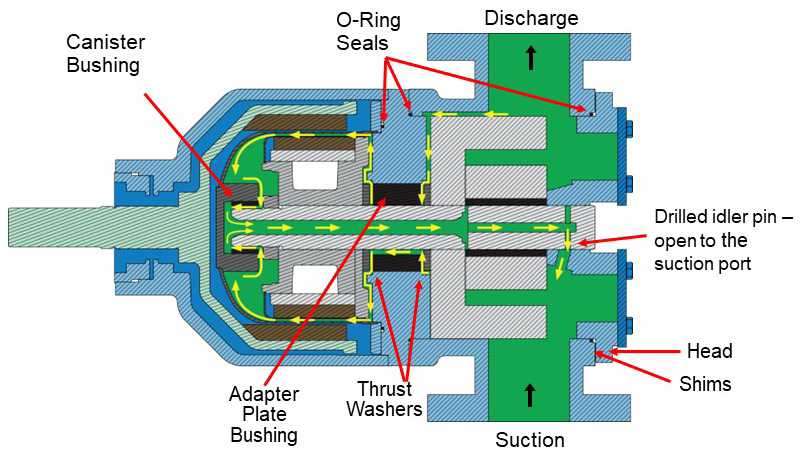
Fig. 2 – UMD Cutaway Image
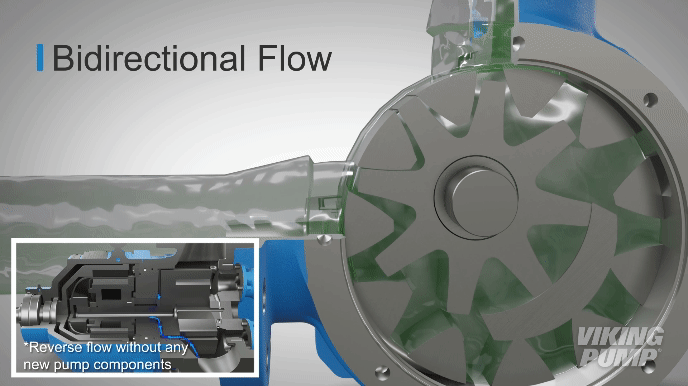
The pumps’ heads can be rotated to four different positions to enable unique port locations. And the reversible direction of flow enables either left- or right-hand suction ports or loading and unloading using the same pump. This is facilitated by thrust washers on either side of the adapter plate that absorb thrust regardless of which direction the pump is turning.
A broad range of viscosities can be handled, from 0.1 to 55,000 cSt, thanks to the high strength magnets. The UMD offers lower cost, lower torque magnet options for very low viscosities or higher torque magnets, up to 900 ft-lbs, for very high viscosities. End clearances for different viscosities are easily set by shimming the head. The standard neodymium magnets enable temperatures from -120⁰F to 225⁰F (-85⁰C to 107⁰C) or samarium cobalt magnets can be used up to 500⁰F (260⁰C).
And to match the 124A/123A/127A Series™ (dynamically sealed model) performance, the 8124A/8123A/8127A (cast iron/steel/stainless steel) Series™ UMDs offer the same maximum capacities from 15 to 500 GPM (3.5 to 114 m3/hr).
UMD Models | Performance | Standard Ports | |||||
Cast Iron | Steel | Stainless Steel | Max Speed, RPM | GPM | m3/h | Size, Inches | Type |
H8124A | H8123A | H8127A | 1750 | 15 | 3.5 | 1.5 | NPT* |
HL8124A | HL8123A | HL8127A | 1750 | 30 | 7 | 1.5 | NPT* |
K8124A | K8123A | K8127A | 780 | 80 | 18 | 2 | NPT* |
KK8124A | KK8123A | KK8127A | 780 | 100 | 23 | 2 | NPT* |
L8124A | --- | --- | 640 | 135 | 31 | 2 | NPT |
LQ8124A | LQ8123A | LQ8127 | 640 | 135 | 31 | 2.5 | Flange |
LL8124A | LL8123A | LL8127A | 640 | 170 | 39 | 3 | Flange |
LS8124A | LS8123A | LS8127A | 640 | 200 | 45 | 4 | Flange |
Q8124A | Q8123A | Q8127A | 520 | 300 | 68 | 4 | Flange |
QS8124A | QS8123A | QS8127A | 520 | 500 | 114 | 6 | Flange |
*8123A Series™ and 8127A Series™ models standard with flanged ports |
Fig. 3 - UMD Models and Performance
So if you’re handling hazardous or flammable liquids, or simply want to stop adjusting packing or replacing mechanical seals to prevent unplanned downtime, ask your Viking Pump Distributor about the UMD drop-in alternative. Whether a new installation or to replace existing Viking pumps, the UMD provides top-of-the-line performance and reliability. Existing pump replacement can be done quickly without the need for new baseplates, motors or gear reducers. What could be simpler?
For more information on Viking Pump’s Universal Mag Drive, check out this video on our YouTube channel: