ORIGINALLY PUBLISHED IN PUMP ENGINEER ON JUNE 6, 2022
“I want you to come listen to a pump for me.”
Customers don’t ask me to listen to quiet pumps. This is symptom #1 of a cavitating pump. The pump is loud. Descriptors like “growly”, “rumbling”, or “gravelly” are used to describe the atypically loud sound coming from the pump.
“Does it always sound like this?” I ask.
“No, it was fine in the fall, but it’s been loud all winter.”
This is symptom #2. The noise is intermittent. It’s loudest when the liquid is more viscous, the supply tank is near empty, when the pump is run faster, the strainer hasn’t been cleaned, etc. The noise is loudest when the inlet conditions are worst.
“How’s flow?”
“Slow. It takes longer to empty the tanks when the pump sounds like this.”
This is symptom #3. The flow rate is lower than expected. This is best confirmed with a meter, but it’s common that this information is more anecdotal: “pump is slow”, “it takes longer to move product”, etc.
There is cause for concern beyond the annoyance of noise and the inconvenience of reduced flow. Over time, cavitation can result in pitting and wear to critical pump internals (see figure 1), resulting in unplanned downtime and costly repairs. These symptoms are a call to action to address cavitation before more serious problems arise.
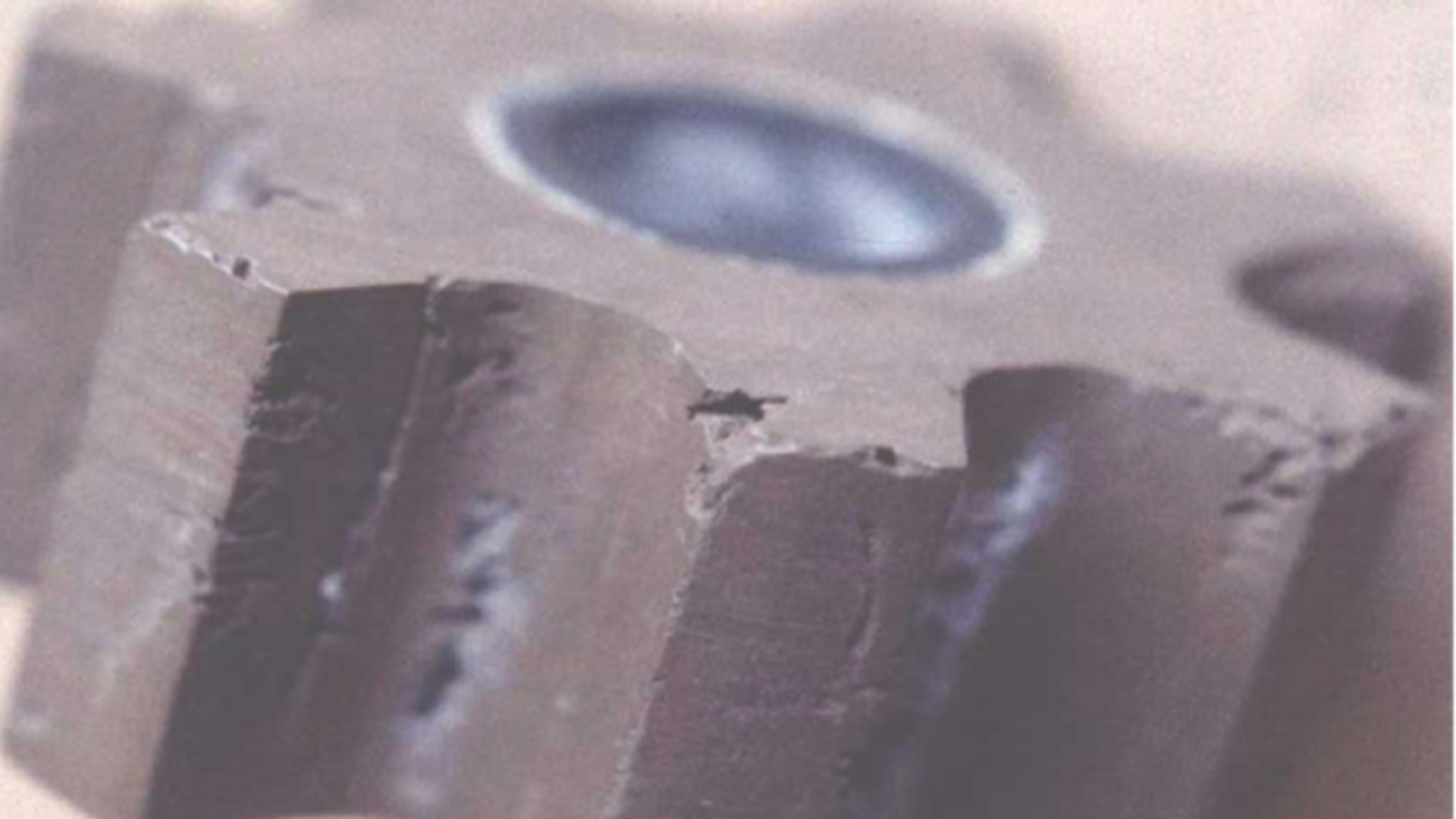
Pump cavitation is the result of inadequate NPSH (net positive suction head).
NPSH available (NPSHa) is a quantifiable value for the absolute pressure* at the inlet port of the pump minus the liquid’s vapor pressure. It must be calculated (more on this shortly).
NPSH required (NPSHr) is a measured value for the absolute pressure* required by the pump to prevent the pump from cavitating. This value comes from testing by the pump manufacturer and is often included with the performance curves.
* For kinetic pumps, like centrifugal pumps, head is used (commonly in units of feet or meters). For positive displacement pumps, like gear pumps, pressure is used (commonly in units of PSI, bar, or feet of water).
NPSH available must be greater than NPSH required to prevent cavitation. If not, vapor-filled cavities form in the inlet of the pump and are carried by the rotation of the pump to the outlet side. Here, exposed to high discharge pressure, these cavities collapse. See figures 2 and 3 from a video of an internal gear pump with a clear head to facilitate view of the gears. In figure 1, the pump is running under normal conditions, the pump is running quietly and at full capacity. In figure 2, the suction valve has been almost entirely closed to create a low NPSH available condition. As a result, vapor bubbles are created at the left, carried by the pump rotation counterclockwise to the outlet side where, exposed to high pressure, they collapse. This collapsing of vapor cavities results in noise and loss of capacity.
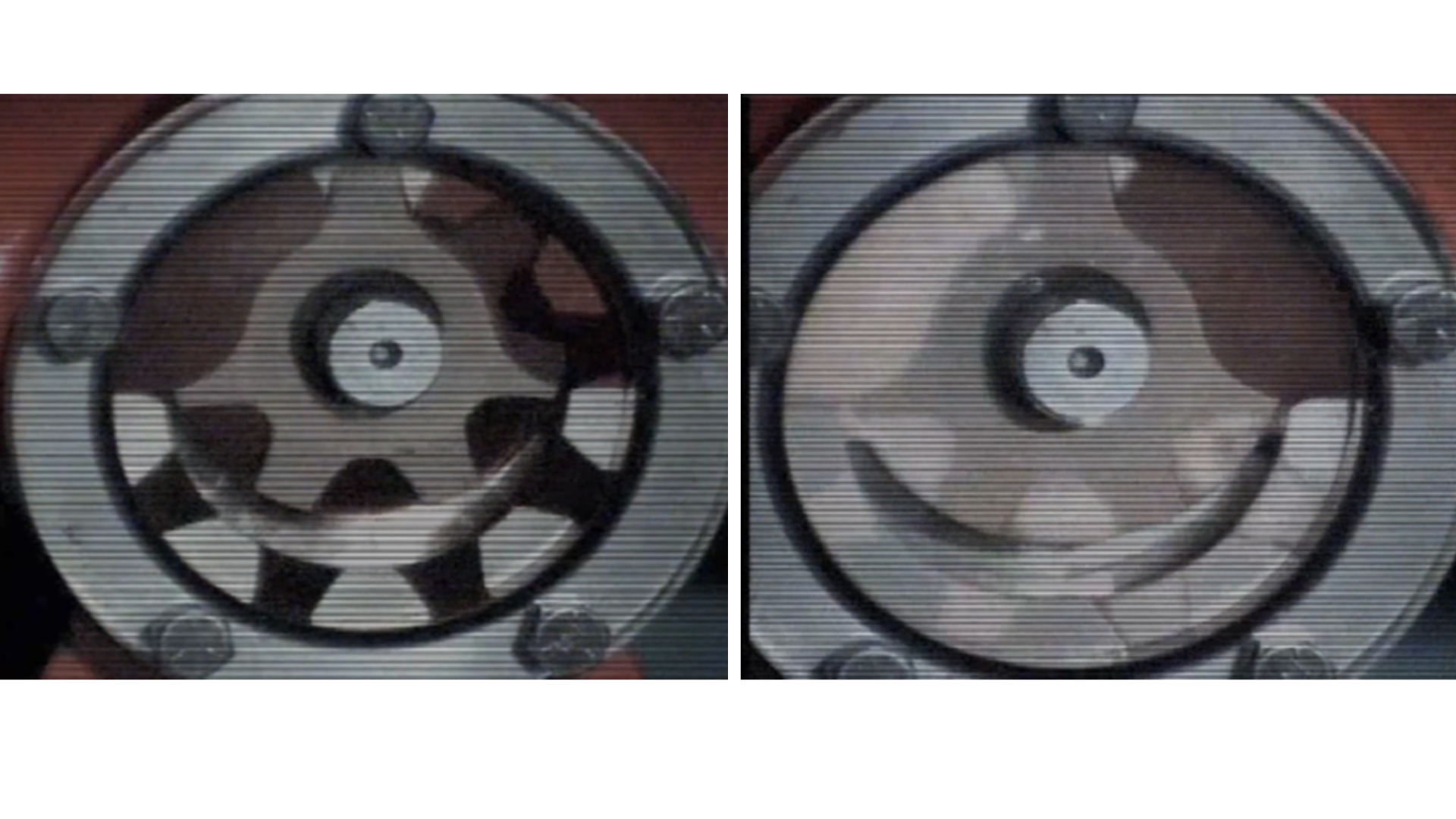
What if your pump exhibits these symptoms of noise and loss of capacity?
Individually, these symptoms could be due to other root causes including wear, relief valve bypass, or aeration. An inexperienced troubleshooter (someone who “knows enough to be dangerous”) may guess that cavitation is the root cause, and often they’ll be right. But before making sweeping changes to the piping or pump it’s best to verify this hypothesis with calculation and/or testing.
Let’s start with how NPSH available is calculated. The equation is as follows:
NPSHa= Ha±Hz-Hf-Hvp
- Where NPSHa is net positive suction head available.
- Ha is applied pressure at the surface of the liquid. For liquids pulled from vented tanks, drums, totes, trucks, etc. this value is equal to atmospheric pressure in absolute units. Atmospheric pressure varies with altitude, so pumps at higher altitudes are often more prone to experiencing cavitation issues than those near sea level.
- Hz is pressure due to the vertical distance between the surface of the liquid in the supply tank and the centerline of the inlet port of the pump. If the liquid level is above the pump (static suction head), this value is added, increasing NPSHa. If the liquid level is below the pump (suction lift), this value is subtracted, decreasing NPSHa.
- Hf is total friction losses in the pipes, valves, fittings, strainers, etc. from the tank to the pump inlet. It’s always subtracted, further decreasing NPSHa.
- Hvp is the vapor pressure of the liquid at the pumping temperature. It’s always subtracted, further decreasing NPSHa. The higher the vapor pressure, the easier it is to transition to a gas, causing cavitation.
- It’s important to note that while any units can be used (PSI, bar, ft. of water, etc.), they do need to be held consistent for each of these coefficients.
Calculations are always recommended prior to pump selection, but once a pump is installed this exercise may be moot. First, variables may be different than what the original datasheet shows. Viscosity may vary, the roughness/inner diameters of the piping system may be in worse than “like new” condition, a valve may be partly closed, or some other obstruction may be hidden inside the pipes. Running these calculations may help to give you an idea of that the NPSH available should be, but once a system is up and running it makes more sense to take a direct measurement.
By installing a suction gauge at or near the inlet port of the pump, the pressure at the pump can be measured. By converting this value to an absolute pressure (adding atmospheric pressure) and subtracting the liquid’s vapor pressure NPSH available can be derived.
This NPSH available value would still need to be compared to the NPSH requirement of the pump provided by the manufacturer. If NPSH available (calculated and/or measured) is less than NPSH required, then this confirms that our original hypothesis is correct, and the symptoms of noise and loss of flow are being caused by cavitation.
So now what?
There are two paths to follow when addressing cavitation.
The first is to improve NPSH available. Looking at the equation above there’s little that can be done to address Ha (atmospheric pressure, usually) or Hvp (vapor pressure). This leaves only opportunities to improve Hz (pressure due to head) and Hf (friction losses).
To improve Hz:
- Raise the minimum liquid level in the supply tank.
- Lower the pump, if possible.
To improve Hf:
- Reduce the length of inlet pipes
- Increase the diameter of inlet pipes
- Reduce the viscosity of the liquid by heating the liquid and insulating the tank and pipes
- Make sure lines and strainers are clean and free from buildup which may restrict flow
Of course, the second path could be to reduce the pump NPSH requirement.
To reduce NPSHr:
- Slow the pump speed. This has the effect of reducing flow. If cavitation is only occurring intermittently (i.e. when the tank is near empty or the viscosity is high) then speed can be dialed down either manually or using logic controls.
- Increase the pump size to hold flow at a lower pump speed.
Some users will accept the symptoms, learning to live with excess noise and decreased flow. But these symptoms may be early indicators of problems down the road. It’s important to understand the signs of cavitation and how to diagnose so that it can be addressed to avoid downtime and cost on the horizon.