External Gear Pump vs Energy Exchange Pump
Viking Pump's GB-410 and GB-414 Series™ were designed specifically to handle the gas dehydration challenges of today.
Energy exchange pumps were a great solution... 70 years ago. As technology continues to advance, so does our understanding of pump efficiency and how electric motor driven external gear pumps are the obvious choice for glycol applications.
Built for Glycol, Built to Last
The ultimate durable, reliable, field-rebuildable solution for your high-pressure oil and gas processing needs. With its hardened parts for enhanced wear resistance, it was engineered specifically for overcoming the challenges of upstream and midstream oil and gas processing applications such as natural gas & CO2 dehydration (glycol), LACT – pipeline injection, gas sweetening (amines), pigging, and condensate transfer.
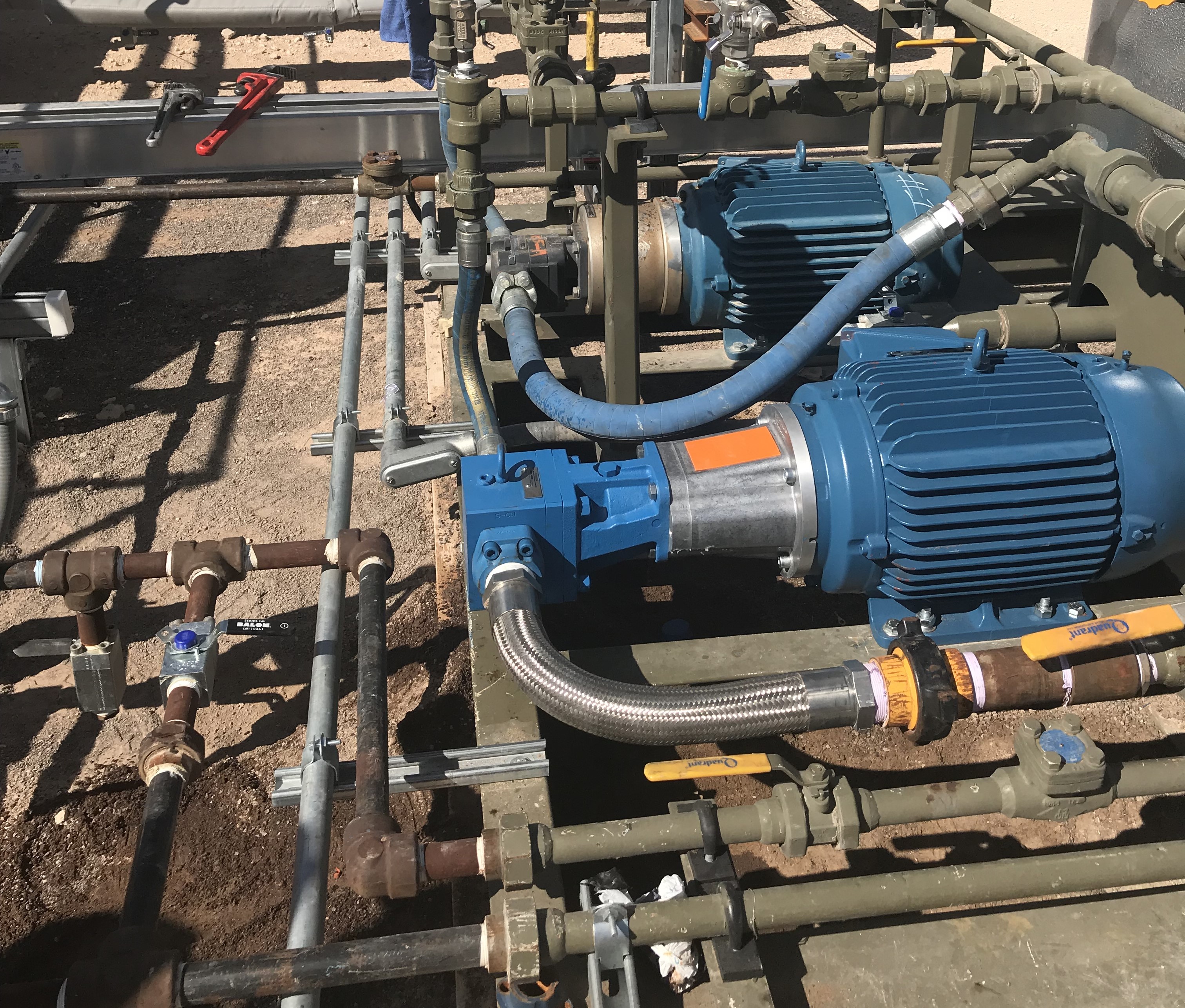
Questions?
Our experienced team is ready to help. Between seasoned sales professionals, expert design engineers, and application engineers we are confident that we can find the best fit for your glycol operation.
Rebuildable Design
When other brands break down, you'll likely find yourself purchasing a brand-new pump that will take weeks to arrive at your facility and then additional days to install... and then you'll repeat that process every time you encounter a failure.
Our Glycol Pump was designed specifically for this application and as such, all wear components are easily replaceable and available in rebuild kits. The simple disassembly & reassembly process makes field service and repair quick and painless.
Related Articles
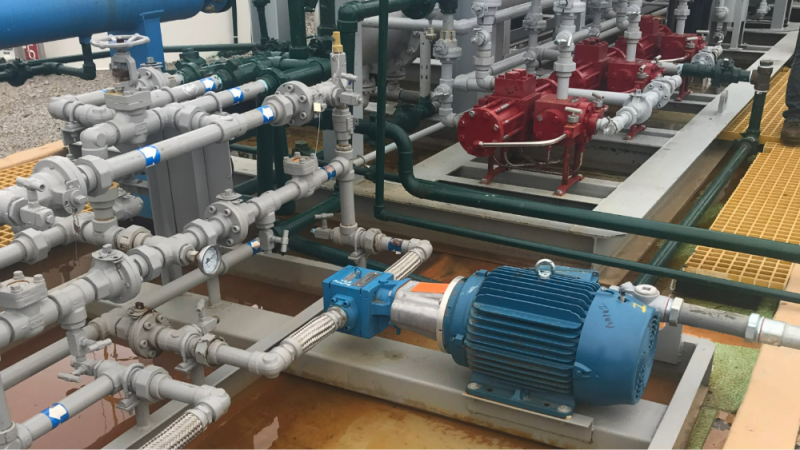
U.S. EPA Bans Natural Gas-Driven Pumps
A new EPA rule, published December 2, 2023, covering new and existing oil and gas operations, requires the use of zero-emissions pumps instead of natural gas-driven pumps, with very few exceptions. It also restricts other natural gas-driven equipment, limits fugitive emissions and calls for reduced flaring of associated gas
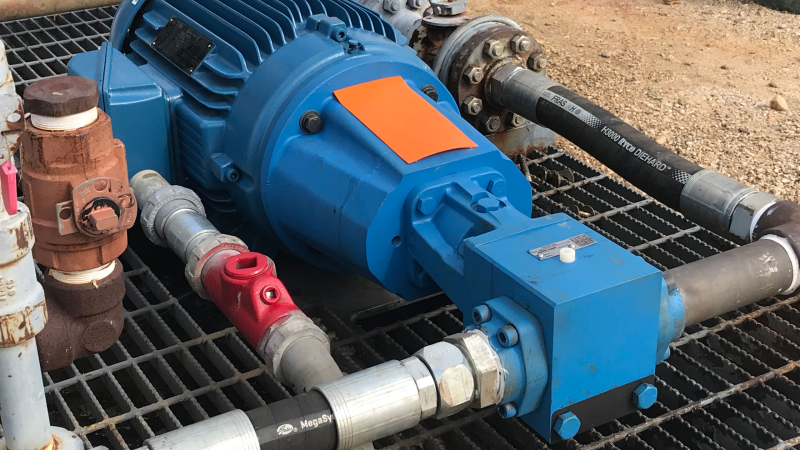
Driving Natural Gas with Glycol Pumps
Industrial gear pumps have many uses in a wide array of market applications—ranging from food processing to pouring asphalt. A growing area in need of specialized gear pumps is in the oil and gas industry, particularly with regards to the removal of water from natural gas via dehydration. Viking Pump entered this market to support customers striving to deliver high-quality product 24/7 to their end users in the face of rising global natural gas consumption. This increasing demand is expected to continue through 2040, due to population growth, coal displacement by cleaner energy, fracking, etc.
How An External Gear Pump Works
First invented nearly 400 years ago, the external gear pump principle is one of the earliest and simplest pump designs. Viking Pump is a leading manufacturer of external gear pumps, with model sizes and designs to cover a wide range of pumping applications, including glycol.
The external gear pump uses two identical gears rotating against each other. One gear is driven by the motor; this gear is called the driver gear. A second, driven gear, meshes with, and is rotated by, the driver gear.
As the gears come out of mesh, they create an expanding volume on the inlet side of the pump. This creates a vacuum which pulls liquid into the pump. Liquid is trapped between the gear tooth cavities and the close fitting casing wall. The rotation of the gears carries the liquid around to the outlet side of the pump. The liquid does not pass between the gears.
At the outlet, the meshing of the gears forces the liquid through the outlet port. Because the gears are supported on both sides, external gear pumps are routinely used for high-pressure applications including hydraulics and pipeline injection.
They come in many sizes to accommodate a wide variety of high speed, high pressure applications.
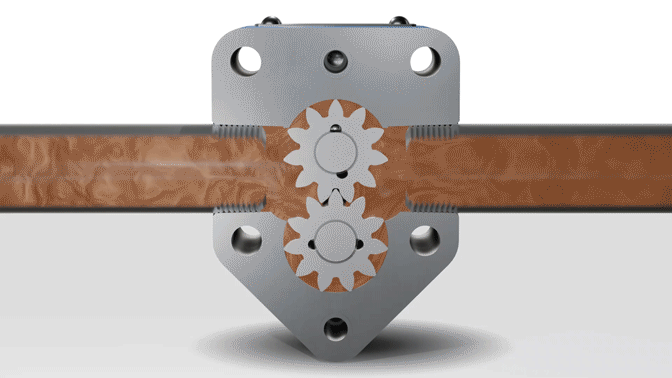
A Recap
GB-410 Series™ | Energy Exchange Pump | |
---|---|---|
Design | Modern, engineered specifically to address today's natural gas dehydration challenges. | Developed 70 years ago and hasn't changed since. |
Temperature Rating | Up to 350°F, including a 225°F delta for temperature spikes. | Starts failing around 200°F. |
Flow Rates | Over 128 gallons per minute. | Up to 7 gallons per minute. |
Maintenance | Easily rebuilt in the field. | Need a hot permit to take the pump to a service center, extending downtime. |
Emissions Contributions | Electric-driven, keeping emissions to an absolute minimum. | Gas-driven, requiring flaring and venting of pollutants. |
Additional Resources
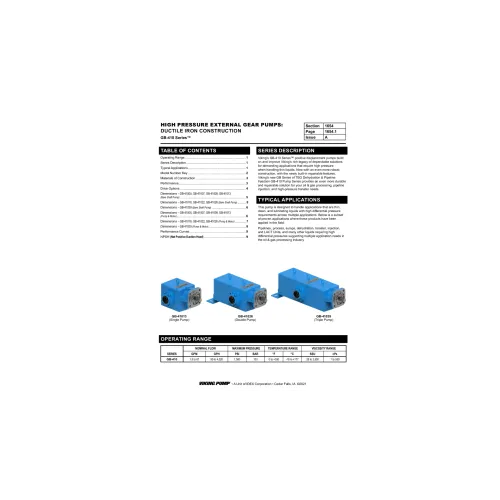
Heading
Catalog Section 1654
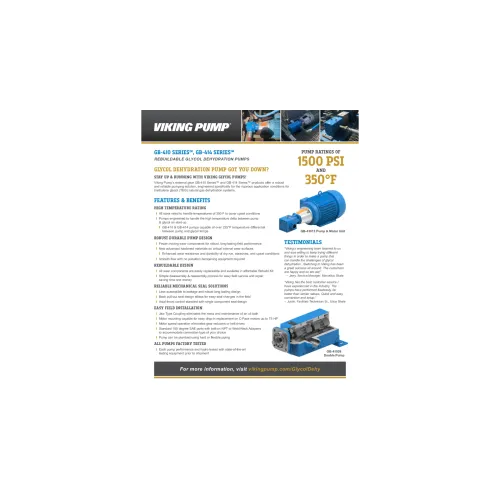
Heading
Glycol Dehydration Flyer
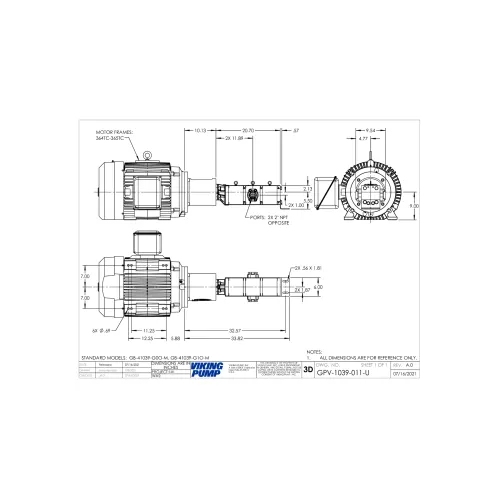
Heading
Drawings
Videos
VERTICALLY INTEGRATED PRODUCTION PROCESS
Viking Pump® operates a local foundry, a 250,000+ sq. ft. machining, assembly and testing center, and an extensive product engineering and testing lab in its world headquarters in Cedar Falls, Iowa, USA. This level of vertical integration ensures maximum quality, ability to satisfy special needs, and to meet project schedules.