Everyone in the oil and gas industry knew it was coming. The end of “free” energy, using natural gas pressure to operate pumps for glycol gas dehydration and general liquids transfer. Because it is actually anything but free. The costs include lost sales gas revenue and release of hazardous air pollutants and greenhouse gases.
A new EPA rule, published December 2, 2023, covering new and existing oil and gas operations, requires the use of zero-emissions pumps instead of natural gas-driven pumps, with very few exceptions. It also restricts other natural gas-driven equipment, limits fugitive emissions and calls for reduced flaring of associated gas. See the EPA methane regulation at https://www.epa.gov/controlling-air-pollution-oil-and-natural-gas-operations/epas-final-rule-oil-and-natural-gas for details.
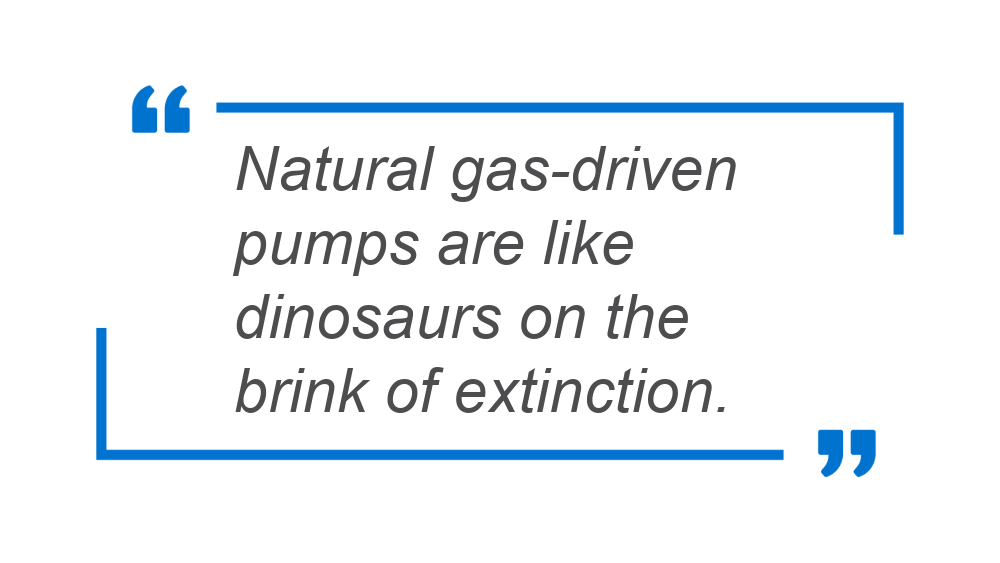
How Gas-Driven Pumps Work & Impact
Virtually all natural gas-driven pumps are reciprocating positive displacement pumps. They operate on the pressure differential between gas line pressure and atmospheric pressure. On the discharge stroke, high pressure natural gas moves a piston or diaphragm to expel liquid on the other side, then on the suction stroke that natural gas is released to atmosphere.
The result is that methane, a powerful greenhouse gas thirty times more potent than CO2, along with other contaminants like CO2, NOx, SO2, H2S and BTEX exhaust are either vented into the atmosphere, or sent to a flare and literally sent up in smoke. This is hazardous for operators, and when multiplied by an estimated 40,000 dehydration plants in the U.S. alone, for the population at large.
One key application for natural gas-driven pumps has been liquid desiccant dehydration of natural gas, which takes water out of the gas to prevent corrosion and hydrate formation that can plug gas lines. In this process, lean (with little or no water) triethylene glycol (TEG), is pumped into a contact tower full of natural gas at line pressures up to 1500 PSI, where it absorbs water and vapor entrained in the gas. This rich (water-laden) glycol then flows to a reboiler where the water is vaporized, and the hot glycol is then pumped back to the contact tower in a closed loop. Gas-driven glycol pumps, also known as “energy-exchange” or “pneumatic” pumps, were the only way to accomplish this dehydration process before electricity was commonly available at well sites. These pumps exhaust their expended drive gas and that gas is then vented or flared into the atmosphere (diagram below).
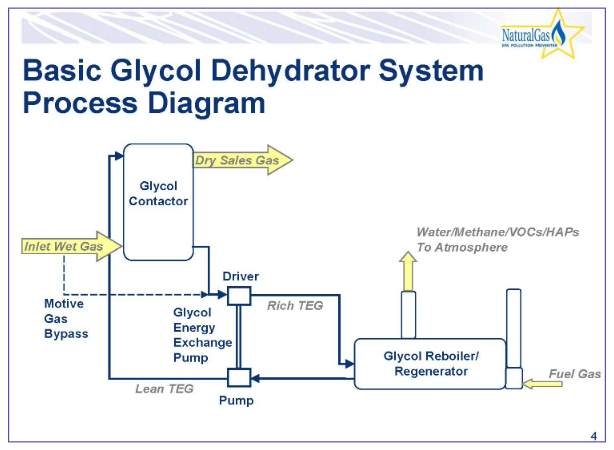
That release of natural gas into the rich TEG is just what the EPA is prohibiting.
Another issue with these pumps is highlighted in the 2006 EPA publication “Replacing Gas-Assisted Glycol Pumps with Electric Pumps,” when they were trying to get users to voluntarily switch. “Furthermore, gas-assisted pumps place high-pressure wet TEG opposite low-pressure dry TEG in four locations with rings on the two pistons and “O-rings” on the central piston connecting rod separating them. As the piston rings becomes worn, grooved, or the O-rings wear, rich TEG leaks past, contaminating the lean TEG. This contamination decreases the dehydrator’s capacity to absorb water and reduces system efficiency. Eventually, the contamination becomes sufficient to prevent the gas from meeting pipeline specifications (commonly 4 to 7 lb of water per MMcf). As little as 0.5 percent contamination of the lean TEG stream can double the circulation rate required to maintain the same effective water removal. In some cases, operators can over circulate the TEG as the dehydrator loses efficiency, which in turn, can lead to even greater emissions.”
These energy-exchange pumps consume between 1.7 scf and 8.3 scf of sales gas per gallon of lean glycol flow, meaning a single pump could be consuming hundreds of dollars a day. That amounts to hundreds of thousands of dollars annually in sales gas loss!
The Solution: Zero-Emission Pumps
The alternative, or in EPA-speak, the BSER (Best System of Emission Reduction) is the use of Zero-Emission Pumps, which are typically electric motor-driven rotary positive displacement pumps rather than gas-driven reciprocating pumps. Rotary pumps are capable of even higher pressures than gas-driven pumps, offer a broader range of flow rates and eliminate the pulsation common to reciprocating pumps.
Motor-driven rotary positive displacement pumps like Viking’s GB-410 Series™ and GB-414 Series™ eliminate virtually all of the negatives associated with gas-driven pumps for glycol dehydration, while overcoming all of the challenges of this application, including high pressure, high temperature, varying viscosity, abrasives and remote 24/7 operations. With thousands of successful installations across all major gas plays, these pumps offer capacities from 2.5 to 128 GPM (9.5 to 485 lpm) at up to 1500 PSI (103 bar) differential pressure. Their unique design helps prevent lockup from thermal shock at startup, a common mode of failure for other rotary pumps, whose gears may expand faster than the casing when hit with hot fluid. When that happens the spinning gears contact the casing, head, and/or bracket, galling and destroying the pump.
Viking TEG pumps are rated to 350⁰F (176⁰C) and can withstand up to a 225⁰ thermal differential without contact, simplifying dehydrator startup routines that otherwise would require slowly warming the pump under low pressure through a bypass. This capability is documented in this video:
Additional Applications: Natural Gas Liquid Transfer to Storage
Another common gas-driven pump application is transfer of Natural Gas Liquids (NGLs) to storage or from storage to tanker truck. Liquid transfer operations are often done with Air Operated Double Diaphragm (AODD) pumps that have been adapted to run on natural gas instead of compressed air. For these pumps the inlet natural gas must be filtered and reduced to around 100 PSI (7 bar), which is also the maximum discharge pressure for these pumps. AODD pumps exhaust significant volumes of motive natural gas directly to atmosphere.
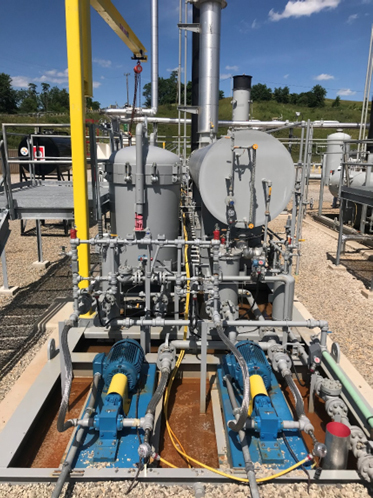
Viking Pump offers motor-driven alternatives here, including rotary PD internal gear, external gear and vane pumps which have gentle suction and low Net Positive Suction Head Required (NPSHr) to minimize flashing on volatile gas condensate, yet have higher flow and pressure capabilities than AODDs.
Like all Viking pumps, flow rate is directly proportional to speed, regardless of developed pressure, providing easy flow rate control. They offer the choice of mechanical seals or sealless magnetic drives.
The world is changing, and natural gas-driven pumps are like dinosaurs on the brink of extinction. As the new EPA rules against them come into effect, operators need to begin their conversions to zero-emission pumps along with all of the other changes to equipment and operations that are required. Viking Pump’s Energy Team, and their Authorized Distributors, are experts in these applications and will be happy to assist you in making the necessary conversions to zero-emission pumping.